Categories: Featured Articles » Novice electricians
Number of views: 55494
Comments on the article: 0
How to learn to solder
The more complex the chain, the more connections. If at least one contact is broken ...
When drawing up and installing an electrical circuit, it may be necessary to connect its parts and elements using terminals, clamps, plugs and sockets, thrust and threaded contacts and other special devices, and sometimes just twisting the bare ends of the connecting wires. Even in the simple electric circuit of a flashlight, you will count about a dozen such connections.
And the electrical circuits of household electrical appliances, tape recorders, televisions contain hundreds and even thousands of interconnected parts.
And each of these compounds should not only be mechanically strong, but also provide reliable electrical contact.
It is not so simple at all. If the conductors at the junction are not tightly pressed against each other or if their surface is covered with a film of oxides that conducts poorly electric current, then with an apparent strength of the connection it will be unreliable. And you already know that it is only in one place in the circuit to break the contact, how the current will stop and the device you made will stop working.
How to ensure the strength and reliability of numerous connections of elements and parts in complex electrical circuits?
One of the most widely used methods for such a compound is soldering. When soldering, the surfaces of the metal parts to be joined are heated and then coated molten solder - a special fusible alloy. Solder fills the space between the connected conductors and partially dissolves in them. This provides after hardening of the solder mechanical strength and good electrical conductivity of the junction.
For soldering parts made of tin, copper and brass, solders are used, which are an alloy of tin with lead or tin with lead and bismuth. The most commonly used are tin-lead solders of the POS-40 and POS-60 grades (respectively with a 40- and 60 percent tin content), as well as POSV-33 tin-lead-bismuth solder. POS-40 solder melts at a temperature of 235 ° C, and POS-60 - at 183 ° C. POSV-33 solder has a melting point of about 130 ° C - it is used to solder parts and elements that do not allow overheating.
Solder can be bought at electrical goods stores. It goes on sale in the form of rods or wire with a diameter of 2-2.5 mm.
The surfaces of the soldered parts are pre-cleaned of dirt and oxide film. However, when heated during soldering, they can again be coated with a thin layer of oxides, which affects the quality of the connection. To prevent this from happening, apply when soldering fluxes - inproducts protecting the surface of soldered parts from further oxidation. The most common flux is rosin.
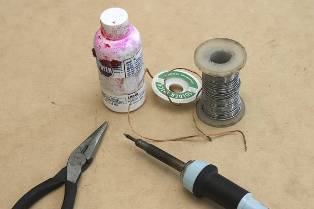
Your main tool when soldering electrical connections is soldering iron. Let's get acquainted with its device and action.
Electric soldering iron - This is the "sibling" of an electric iron, tile, kettle and other household electric heating appliances. The action of such devices is based on the release of a large amount of heat during the passage of electric current. The main part of the soldering iron is a copper rod with a pointed tip - a “sting”, inserted into a metal tube around which a heating element is located (a nichrome spiral in a shell made of heat-resistant insulation - mica or ceramic). The ends of the spiral of the heating element are connected to insulated copper wires - a cord that is led out through a hollow plastic handle and ends with a plug. The heating element is covered by a casing on top.
When the soldering iron is turned on in the electric network, the current passes through the nichrome spiral and heats it.The generated heat is transferred to a copper rod, which is heated to a temperature of 300 - 350 ° C. By touching the hot tip of the soldering iron, you can melt the solder pieces and heat the surfaces of the soldered parts to the temperature at which the soldering is carried out.
The industry produces electric soldering irons of various shapes and sizes. Many of them are designed for inclusion in a network with a voltage of 220 V.
In addition to the danger of electric shock, the risk of burns and fires is fraught with careless handling of the soldering iron. The metal casing and the copper rod of the soldering iron are heated to high temperature. This must always be remembered. Keep a heated soldering iron only by the plastic handle. It is necessary to ensure that the vinyl insulation of the wires through which the current is supplied to the soldering iron does not accidentally touch the hot casing or the rod, because with such contact the insulation will melt and a short circuit may occur.
In the intervals between soldering, you can put the soldering iron only on the base of non-combustible material: asbestos, ceramics, etc. But it is better to make a special stand for the soldering iron, providing in it not only a place for its convenient location, but also small recesses for the materials necessary for soldering - solder and rosin.
It is impossible to ignore the fact that the pairs of solder and flux formed during soldering have a harmful effect on the human body. Therefore, you can not continuously solder for a long time, and during breaks do not forget to ventilate the room well.
Before soldering, the device should be prepared for operation. With the help of a file, its working part - the sting - must be ground at an angle of 30 - 45 ° and cleaned. Then it must be tinned.
To do this, include a soldering iron in the network and, when it is slightly heated (after 1-2 minutes), cover the sting with a layer of flux, pressing it to a piece of rosin. Spreading over the surface of the sting, rosin protects it from oxidation during further heating. As soon as the tip is heated to the melting point of the solder (this can be determined by touching a piece of solder), the working surface is covered with solder.
Please note that overheating of the soldering iron before coating the tip with rosin is unacceptable. If, nevertheless, for any reason, the soldering iron overheats and the protected part of it is covered with a dark blue coating of copper oxide, then it should be turned off, cooled and cleaned again, and then proceed to tinning first.
Metal surfaces prepared for soldering should be thoroughly cleaned of oxides and fats and tinned. They clean the places of soldering with a knife, sandpaper or a file. When tinning, a flux layer is first applied to the metal surface, and then with a hot soldering iron with a small amount of solder on the sting several times along the tinned surface, helping the solder to spread and moisten it with a thin and even layer.
When soldering mounting joints, a flux layer is first applied to the junction. Then solder and a soldering iron tip are simultaneously applied to this place. The solder bar is held in the left hand (it is better to hold it with tweezers so as not to burn your fingers, since it also heats up during soldering), and the soldering iron handle is in the right.
To quickly warm the junction to the melting point of the solder, the soldering iron is first applied not with the tip of the tip from which the solder flows, but flat so that the contact area is the largest. After holding the soldering iron in this position for no more than a second, the solder is distributed with a sting along the entire surface of the joint.
The molten solder can be transferred to the place of soldering and soldering iron tip. To do this, it is pre-dipped for a split second in rosin and a drop of solder is placed in the box on the stand. The amount of solder required for soldering should be minimal. Solder should fill the junction from all sides.
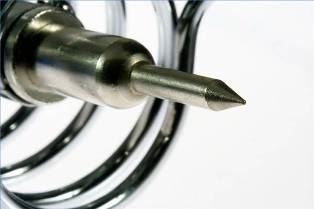
When soldering, maintaining a soldering iron is important.The surface of his sting should be smooth, free from soot (oxide) and well tinned. The soldering iron should be heated to the required temperature, depending on the brand of solder. A temperature regime is considered normal when the solder melts quickly, but does not drain off the tip of the soldering iron; rosin does not burn instantly, but remains on the sting in the form of boiling droplets.
Overheating of the soldering iron is unacceptable, as this leads to the oxidation of the tip and the appearance of shells on it. But it is also impossible to work with an insufficiently heated soldering iron: the connections are fragile and unreliable.
Now, taking into account all our tips and tricks, practice soldering by combining pieces of copper wires with a diameter of 0.8 - 1.5 mm using this method.
First remove insulation from the ends of the conductors. Then strip the ends with a knife to a length of 8 - 10 mm and tin. After that, attach the ends of the conductors to each other and solder. With high-quality soldering, the solder covers the junction with an even layer with a smooth and shiny surface. The uneven and grainy surface of the junction is a sign of insufficient heating of the soldered parts.
Soldering a variety of shapes from pieces of copper wires can be a good training exercise in the practical development of soldering.
Read also:Induction Soldering Stations
See also at bgv.electricianexp.com
: